Toyota Motor Corporation in 2003
|
|
ICMR HOME | Case Studies Collection
Case Details:
Case Code : BSTA053
Case Length : 24 Pages
Period : 2004
Organization : Toyota Motor Corporation
Pub Date : 2004
Teaching Note :Not Available Countries : Japan
Industry : Automobile
To download Toyota Motor Corporation in 2003 case study (Case Code: BSTA053) click on the button below, and select the case from the list of available cases:
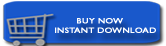
OR

Buy With PayPal
|
Price:
For delivery in electronic format: Rs. 500; For delivery through courier (within India): Rs.
500 + Rs. 25 for Shipping & Handling Charges
» Business Strategy Case Studies
» Case Studies Collection
» Business Strategy Short Case Studies
» View Detailed Pricing Info
» How To Order This Case
» Business Case Studies
» Area Specific Case Studies
» Industry Wise Case Studies
» Company Wise Case Studies
Please note:
This case study was compiled from published sources, and is intended to be used as a basis for class discussion. It is not intended to illustrate either effective or ineffective handling of a management situation. Nor is it a primary information source.
Chat with us

Please leave your feedback
|
<< Previous
Excerpts
Product Development
Product development in the automobile industry was highly capital intensive and time consuming. Yet, auto makers had to keep coming up with new models from time to time. The accepted practice was to standardize the core product, the platform and to build features around a small number of platforms...
|
|
Operations
Toyota's operations had been streamlined over several decades, resulting in the world famous Toyota Production System (TPS). Although TPS had been well researched and written about, other companies including famous Japanese automobile majors such as Nissan had found it difficult to replicate the system...
Kanban
Kiichiro Toyoda, realised the advantage America had over Japan in automobiles. He understood that to catch up with the Americans, Toyota had to master basic production techniques and then reorganize the production system in a unique way...
Jidoka
Another concept which Toyota emphasized was Jidoka, which meant automation with a human touch i.e., investing machines with human like intelligence. Ohno realised it was always better from the point of view of both efficiency and quality to identify the defects as soon as they occurred, rather than at the end of the production line...
Kaizen
Kaizen, another unique feature of the Toyota Production System, meant continuous improvement. Kaizen emphasised looking for better, safer, easier and more efficient ways of working, which could improve efficiency and reduce waste no matter how small the tasks were...
Production Scheduling
During the late 1950s, Toyota also began modifying its daily production schedule and assembly sequencing to ensure that workers produced only what was necessary and the company did not have to store finished vehicles or components for long periods...
Vendor Management
Ohno began coordinating deliveries from subcontractors with production lines in the Koromo factory during 1949 to eliminate intermediate warehousing. He gradually educated these firms and instructed them to deliver only when they received the kanban...
Excerpts Contd...>>
|
|